From Waste to Wealth: How Lead is Extracted from Used Batteries
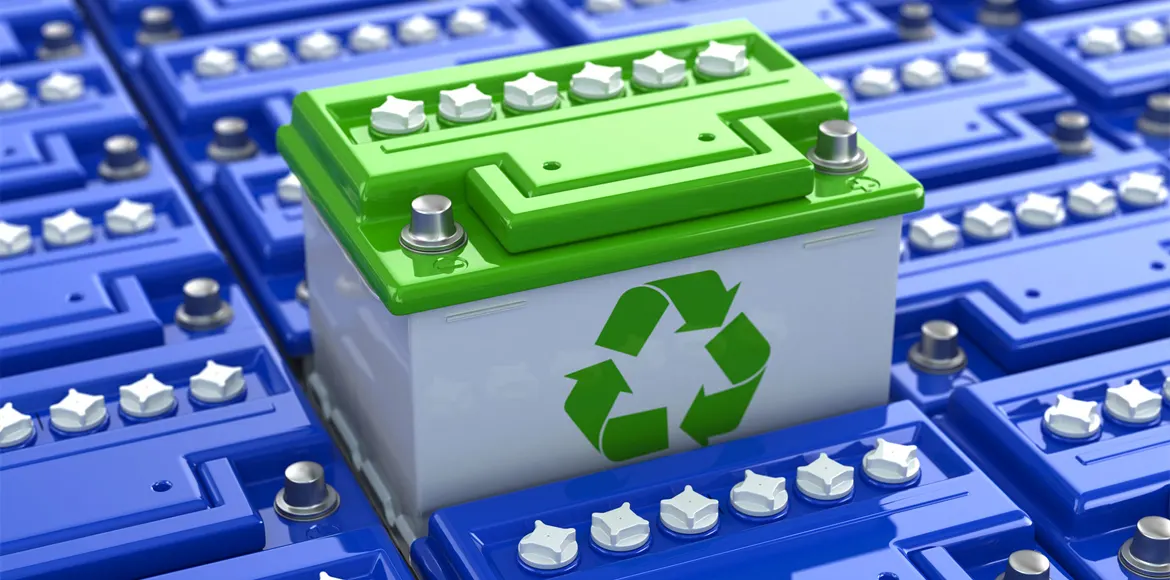
It all begins with the battery itself—typically a lead-acid one, the kind you’ll find under the hood of most cars. When it dies, it doesn’t belong in a landfill. Instead, it’s collected through scrapyards, auto shops, or recycling programs. In the U.S., over 90% of lead-acid batteries are recycled, thanks to a well-oiled system of drop-offs and regulations. That old battery you swapped out last oil change? It’s likely already on its way to a second life.
These batteries are heavy—about 60% of their weight is lead, locked in plates and connectors, with plastic casings and sulfuric acid rounding out the mix. The challenge is pulling that lead out cleanly and profitably, and that’s where the recycling magic happens.
The Extraction Process: Breaking It Down
Once collected, the batteries head to a recycling facility, where they’re dismantled with precision. First, the plastic casing is cracked open and separated—often melted down into pellets for new battery casings or other products. The sulfuric acid is drained and neutralized, turning it into water or useful byproducts like sodium sulfate (think laundry detergent). Then comes the star of the show: the lead.
Kathryn Murphy
The Bigger Picture: Challenges and Promise
Lead recycling is a success story—lead-acid batteries are the most recycled consumer product in many countries—but it’s not flawless. Collection gaps persist in some regions, and illegal dumping still happens. Green tech like hydrometallurgy needs more investment to scale up globally. Plus, not every recycler plays by the rules—shady operations can cut corners and pollute.