Lead Recycling Explained: A Cleaner Alternative to Mining
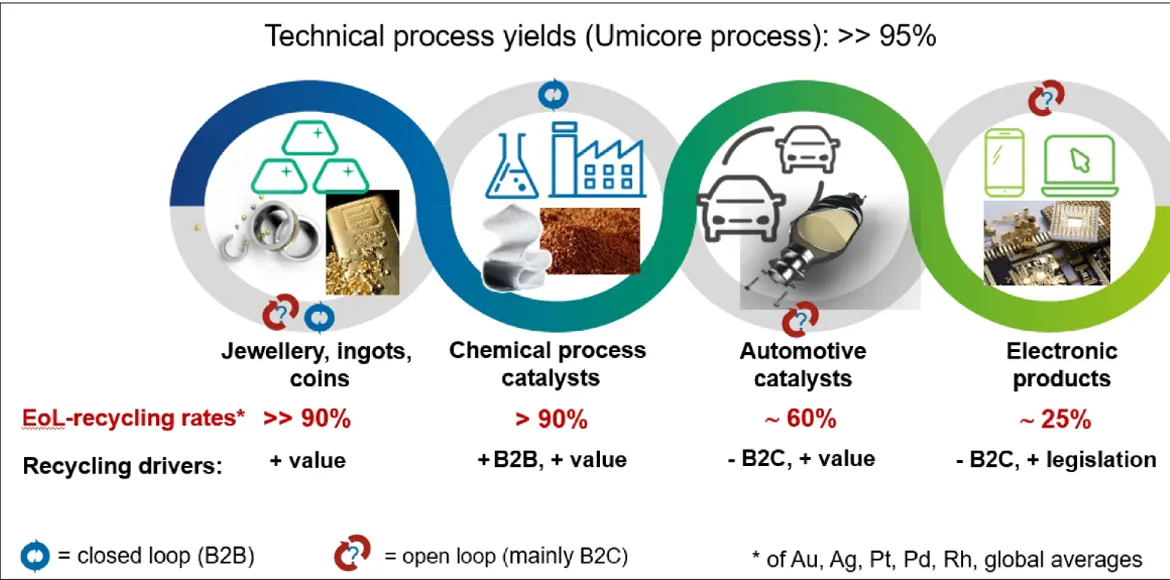
Lead is everywhere—powering car batteries, shielding X-ray rooms, and even lining pipes in some corners of the world. But getting it fresh from the earth is a dirty, costly business. Enter lead recycling: a cleaner, smarter way to keep this valuable metal in play without tearing up the planet. By turning used batteries and scrap into pure lead, recycling is rewriting the story of resource use. Let’s break down how it works and why it’s a game-changer compared to mining
Lead is a workhorse, especially in lead-acid batteries, which power most vehicles and backup systems globally. These batteries don’t last forever, but their lead can—almost indefinitely, if recycled right. Unlike mining, which scars landscapes and pumps out CO2, recycling reuses what’s already here. In the U.S., over 90% of lead-acid batteries are recycled, making them one of the most recycled products around. That’s a stark contrast to the millions of tons of ore dug up yearly to feed demand.
How It Works: From Scrap to Shine
The recycling process starts with collection—think old car batteries from your local mechanic or scrap lead from construction sites. These materials head to specialized facilities where the transformation begins. For lead-acid batteries, the most common source, the steps are clear-cut
Kathryn Murphy
Challenges and the Road Ahead
Lead recycling is a success story, but it’s not perfect. Collection gaps exist—some batteries still slip into landfills, especially in regions with spotty infrastructure. Not all recyclers are equal either; outdated facilities can pollute if they skip proper safeguards. Scaling up green tech like hydrometallurgy takes investment, and public awareness needs a boost to ensure every battery gets recycled.